Les forets carbure
Marché de spécialités
Les forets carbure, plus particulièrement les forets carbure monobloc, ont supplanté le foret HSS dès qu’il s’agit de technologies d’usinage modernes exigeant des vitesses de rotation élevées. Sur ce marché de spécialités, où chaque fabricant propose ses revêtements et géométries propres, optimisés en fonction de la matière, les gammes se doivent d’être larges pour répondre précisément aux besoins.
La réputation du carbure en termes de précision, de rapidité et donc de productivité n’est plus à faire. Adapté aux exigences des technologies d’usinage modernes avec des vitesses de coupe et des avances plus élevées, le foret carbure a donc supplanté le foret HSS acier rapide pour l’usinage des aciers durs, des aciers inoxydables, de la fonte, de l’aluminium ou du titane ainsi que des matériaux composites. Le carbure est en fait une poudre, un composé fritté de carbure de tungstène associé à des métaux de liaison comme le titane, le cobalt ou le nickel avec des proportions différentes selon les propriétés attendues, notifié de K10 à K15 pour l’essentiel des forets du marché, et qui repose sur des recettes spécifiques selon les grands carburiers comme Sandvik Coromant, Walter Titex (qui fait partie du même groupe que Sandvik) ou Gühring.
Plaquettes carbure
En ce qui concerne le foret et les applications pour l’acier, le carbure s’exprime sous plusieurs formes.
Le foret à plaquettes carbure dispose d’un corps en acier rapide auquel ont été rapportées des plaquettes carbures brasées qui renforcent donc les qualités et la précision de perçage du foret HSS, dès qu’il s’agit d’usiner une pièce d’acier dont la nuance se situe au-delà de 33 HRC (environ 1100 N/mm2). Ce type de foret, disponible dans les gammes standard de 1,5 à 20 mm de diamètre, peut s’utiliser sur des perceuses à colonne mais aussi sur des centres d’usinage. En revanche, il ne convient plus pour les aciers très durs où lorsqu’un fort rendement au trou est exigé. De façon générale, pour une utilisation optimisée, un foret carbure s’utilise à des vitesses de rotation élevées, et pas sur une machine électroportative. Fragile et coûteux, il supporte mal les vibrations et risque donc de voir sa durée de vie raccourcie.
Embouts carbure
Dès que la notion de coût au trou de perçage entre en jeu, et qu’il s’agit d’aciers plus durs, dès 45 HRC, et de composites, le foret à embouts carbure et surtout le foret carbure monobloc s’imposent.
Proposant avec des vitesses élevées une productivité supérieure au foret à plaquettes carbure, le foret à embouts ou inserts carbure a vu le jour il y a une quinzaine d’années. Il dispose lui aussi d’un corps en acier HSS dont la tête est ici équipée d’embouts carbure amovibles, avec des géométries et des nuances optimisées pour les différents types d’aciers. Cet aspect amovible lui confère un avantage sur le foret carbure monobloc, sur lequel nous reviendrons plus longuement. Le foret à inserts carbure évite effectivement d’avoir à gérer la question de l’affûtage nécessaire pour que l’outil carbure monobloc retrouve ses performances d’origine, une opération qui peut se produire entre quatre et dix fois dans la vie d’un outil monocarbure et qui exige le retour du foret chez l’industriel. Il suffit de changer l’embout carbure, sans immobiliser l’outil et en évitant les temps morts, les industriels ayant travaillé ces dernières années sur la rapidité du changement des embouts. Néanmoins, les forets à inserts carbure ne sont disponibles que dans des plages de diamètres de 10 à 30 mm, parfois 8 mm, limite technique pour ce genre d’outils.
Foret carbure monobloc
Plus répandu que le modèle à embouts, le foret carbure monobloc, donc le corps est intégralement composé de cette poudre frittée, est devenu un classique des ateliers. Il permet de réaliser un trou en une seule étape, de bien évacuer les copeaux et offre donc un très haut rendement, sachant que la qualité du porte-outil joue également.
Au-delà du mélange qui, comme on l’a vu, obéit à des compositions variées pour optimiser les applications, les différents types de carbure ont soit la forme de micro-grains, ce qui représente 90% des ventes des forets carbure monobloc que l’on retrouve dans la distribution, ou de nano-grains, dits également sub-micro grains. De dimension inférieure au micron, ces grains permettent d’obtenir des arêtes vives, très précises.
80 à 90% des forets monobloc sont revêtus, ce qui leur assure une durée de vie importante et de bonnes conditions de coupe, le revêtement faisant office de barrière thermique. Ce revêtement est de type TiAlN (Titanium aluminium nitride), bien que, là encore, chaque fabricant ait sa propre recette qui varie selon les matériaux à usiner. C’est ce qui explique aussi que la phase de ré-affûtage passe obligatoirement par le fournisseur pour que le foret retrouve le même revêtement.
Profondeur de perçage
Un foret carbure monobloc, comme tout foret d’ailleurs, se définit tout d’abord par sa longueur de perçage, exprimée en nombre de fois son diamètre. Ainsi un foret de diamètre 10 en 5d est en mesure de percer une profondeur de 50 mm. Sur le foret monocarbure, les diamètres démarrent à 0,1 mm, niche dédiée aux circuits imprimés par exemple, jusqu’à 25 mm ou 30 mm pour les produits figurant en catalogue. Certains forets présentent des diamètres supérieurs mais relèvent alors du sur-mesure.
Le cœur de gamme se situe entre 3 mm, pour des applications liées par exemple à l’horlogerie, à 12 ou 14 mm. La distribution stocke souvent les produits standard 3d et 5d qui représentent l’essentiel du marché, avec parfois du 7d et du 10d, sachant que plus un foret est long, plus il est fragile et complexe à utiliser. Il exige notamment une bonne évacuation des copeaux, ce qui peut dans le cas contraire jouer sur la qualité du trou.
Avec ou sans trous d’huile
L’autre paramètre important concerne justement la présence ou pas de trous d’huile intégrés, destinés à assurer la lubrification pendant l’usinage, gage d’une bonne évacuation des copeaux et donc de la qualité du filet et de la durée de vie de l’outil. Dès que le foret dépasse la dimension 5d, la présence de trous d’huile est recommandée. Plusieurs systèmes d’arrosage existent sur le marché. Le système classique, sous émulsion et avec une huile entière, domine largement les ventes, notamment dans le secteur de la distribution.
Le procédé par micro-pulsion, en développement, s’appuie lui sur un mélange d’huile et d’air. L’huile se prouve alors concentrée sur le processus de coupe, ce qui permet de préserver l’environnement de la machine.
Tolérance et précision
Reste que les spécialistes le savent bien, dès que l’on parle d’usinage, de productivité et de précision, on pénètre dans un univers complexe, avec des types d’affûtage, des géométries, des sens de coupe, des angles de pointe de 118°, 120°, 130°, 150° voire plus, etc., souvent spécifiques en fonction des fabricants et optimisés par rapport aux matériaux à usiner, la qualité du trou que l’on veut obtenir... Des éléments qui ne sont pas faciles à appréhender pour un profane, et qui risquent de sombrer dans l’addition de particularités. Il est aussi question de cote, de tolérance de trou... critères évidemment importants dès qu’il s’agit de fabriquer une série de pièces identiques.
Globalement, de la matière à usiner dépend la géométrie. Il existe des géométries universelles, pour la mécanique générale par exemple et des géométries optimisées par rapport à la matière. Le profil de goujure détermine l’aptitude du foret à former, à adapter et à faciliter la remontée des copeaux, variable donc selon les matières, contribuant ainsi à évacuer la chaleur. Le foret universel est souvent polyvalent quel que soit le type d’acier, ce qui évite aussi un cycle de débourrage, alors que la fonte, l’inox, l’aluminium et bien entendu les inconels demandent des géométries dédiées.
Si le foret avec deux lèvres de coupe domine les ventes des articles vendus dans la distribution, à noter que le foret trois lèvres se développe, permettant de travailler plus vite, de façon plus calibrée, avec plus de stabilité et donc de précision. Ils sont également utilisés pour l’aluminium.
Des ventes poussées par le rééquipement
De façon générale, répondant aux exigences de productivité des entreprises, les forets monocarbure sont en plein développement. Un essor qui devrait se poursuivre avec la montée en puissance des centres d’usinage dans les ateliers, au détriment des machines traditionnelles. Et comme le coût d’utilisation de ces machines est élevé, la performance du foret est de rigueur... Et précision oblige, si des standards existent sur ce marché, les gammes restent larges en termes de diamètres, notamment, pour couvrir tous les besoins. D’où une efficacité logistique de la part des fournisseurs avec des capacités de livraison en J+1, les coûts de stock restant importants sur ce type de produit à la valeur unitaire forte. Pour les acteurs du marché, il n’est donc pas pensable de vendre des forets monocarbure juste en complément de gamme.




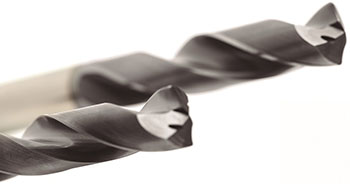

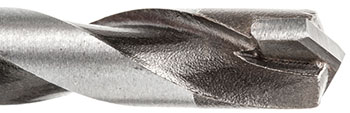




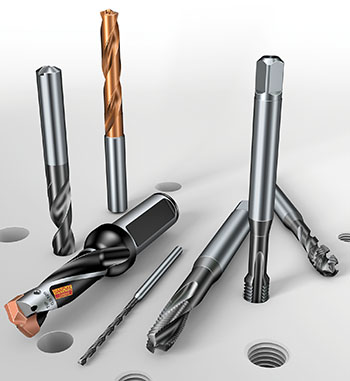
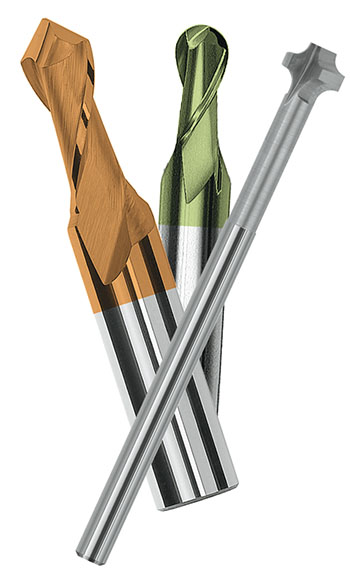