Les torches de soudage
Des outils qui gagnent en ergonomie
Dominées par deux procédés, le soudage MIG et le soudage TIG, les torches de soudage s’inscrivent totalement dans la prise de conscience actuelle concernant les conditions de travail des utilisateurs et les troubles musculo-squelettiques. L’ergonomie de la torche est appelée à devenir un critère d’achat majeur, d’autant qu’elle est source de productivité.
La conjoncture actuelle n’a pas épargné le marché des torches de soudage. Crise dans le secteur de l’automobile ou des travaux publics, fermetures de sites industriels, tous les paramètres sont réunis pour que les ventes de torches de soudage, jugées habituellement stables, accusent en 2012 une baisse de l’ordre de 5% en volume. Pourtant, en 2011, ses acteurs avaient retrouvé des niveaux d’affaires dignes d’avant crise.
Preuve, s’il en fallait, de la sensibilité à la conjoncture de ce produit, les ventes de pièces d’usure (cols de cygne, gaines...) affichent, elles, des baisses d’environ 30%. Comme quoi, en 2012, le renouvellement peine à trouver son souffle. Et ce, même si la torche, considérée souvent comme du consommable, ne subit pas toujours les meilleurs traitements, surtout lorsqu’elle est employée par des mains peu expertes. Jetée par terre, utilisée comme marteau, écrasée par les roues d’un chariot élévateur, il lui est parfois difficile de supporter ce genre d’outrages au-delà de trois mois alors que dans la plupart des cas, elle serait en mesure d’atteindre allègrement les deux ou trois ans de vie. D’ailleurs, certaines entreprises numérotent désormais leurs torches afin de responsabiliser les utilisateurs.
Des applications nombreuses
La baisse des ventes concerne les différents segments de marché, ce secteur étant articulé selon deux procédés majeurs : les torches de soudage MIG/MAG et les torches TIG. Les premières représenteraient en France un volume d’environ 35 000 pièces alors que les secondes se situeraient aux alentours de 15 000 unités. Orientée sur des applications techniques réalisées par des soudeurs expérimentés au savoir-faire sans doute moins délocalisable, la torche TIG souffre sans doute moins que la torche MIG/MAG. Elle officie notamment dans des industries telles que l’aéronautique, l’aérospatial, la pétrochimie ou encore la tôlerie pour le soudage de matériaux fins ou spéciaux comme le titane, l’inox. Plus facile à utiliser, plus polyvalente, la torche MIG/MAG convient pour des soudures moins précises, moins fines dans l’industrie lourde et mi-lourde, comme la construction navale, la fabrication de structures en acier, la réparation et la maintenance, et bien entendu l’industrie de la tôlerie (automobile).
Un arc, pas une flamme
Qui dit soudage, dit assemblage de plusieurs pièces de métaux (une pièce usinée et un métal d’apport) à l’aide d’une source de chaleur. Avec une torche, cette chaleur est générée par un arc électrique, d’où le nom de soudage à l’arc. Rien à voir donc avec le chalumeau, employé en plomberie par exemple, qui provoque une flamme obtenue à partir du mélange de deux gaz pour chauffer et créer une fusion des métaux.
La torche est reliée à un poste à souder, adapté à son procédé (MIG/MAG, TIG) qui va lui donner son énergie et nombre de ses compétences. Il permet notamment de programmer la vitesse de dévidage du fil d’apport en fonction de l’épaisseur à souder pour le procédé MIG ou encore l’intensité du courant. Les systèmes à synchronisation manuelle entre la torche et le poste de soudage, aux réglages parfois complexes, ont depuis quelques années été rejoints par des systèmes de contrôle avec micro-processeur, dits synergiques, beaucoup plus faciles d’utilisation. La torche permet ensuite alimenter la pièce à souder en fil d’apport, en courant et en gaz de protection (elle reliée à une bouteille). La plupart des torches du marché sont à raccord européen et s’adaptent donc à tous les générateurs.
Domination de la torche MIG
Facile à utiliser, même par un soudeur peu expérimenté, la torche MIG/MAG est dite semi-automatique. Le métal d’apport nécessaire à la soudure se présente sous la forme d’un fil embobiné autour d’une bobine logée dans un dévidoir, intégré au générateur ou à l’extérieur si l’utilisateur a besoin d’aller souder loin du poste. Il déplace alors le dévidoir et pas le générateur. Le fil est acheminé directement à travers une gaine jusque dans la zone de soudage. Créé par l’alimentation électrique et déclenché par la gâchette de la torche, l’arc fond le matériau soudé et le fil à souder de façon à créer la soudure.
La nature du fil dépend évidemment de celle du matériau à souder (acier, inox, alu, carbone, alliages spécifiques...). Pendant le soudage, le fil dévidé est conduit jusqu’à l’extrémité du col de la torche, à travers une gaine adaptée au type de fil utilisé. Pour favoriser un coulissement régulier du fil d’aluminium, par exemple, la gaine est souvent conçue en PTFE. La qualité de la gaine est en effet déterminante. Si le fil accroche, se crée alors l’effet de pompage, traduisant un coulissement par à-coups. De plus, s’il est abimé, la qualité de l’arc s’en ressent, ce qui est, dans tous les cas, préjudiciable au résultat de la soudure. Dans l’idéal donc, le soudeur doit disposer de torches différentes en fonction des nuances d’acier, ce qui n’est pas toujours le cas dans la réalité.
Par ailleurs, pour que la soudure dure dans le temps, le bain de soudure en fusion doit être protégé des effets de l’oxydation de l’air ambiant par un gaz de protection. Provenant souvent d’une bouteille, le gaz est diffusé par la torche au niveau de la zone de travail. Avec le procédé MIG (Metal inert gas), c’est un gaz de protection inerte qui est utilisé. Il ne participe donc pas au processus de soudage tandis que le soudage MAG (Metal active gas) repose sur un gaz de protection actif qui, lui, participe au processus. Le mode MIG est le plus couramment utilisé.
Précision du soudage TIG
En ce qui concerne le soudage TIG (Tungsten inert gas), l’arc de soudage se forme entre une électrode de tungstène, non fusible, et la pièce travaillée. Comme pour le procédé MIG, le gaz de protection est un gaz inerte qui protège le bain de soudage contre l’oxygénation.
En revanche, ce n’est pas la torche qui apporte le matériau d’apport dans le bain de soudure mais la main du soudeur, d’où une structure de la torche différente, plus petite. Evaluant lui-même la quantité de métal d’apport nécessaire, l’utilisateur d’une torche TIG doit donc être dûment formé.
Certains fabricants ont fait évoluer la torche TIG en lui adossant un système d’apport automatique du fil situé entre la torche et le poste de soudage, ce dernier gérant directement la quantité de fil nécessaire sur l’arc. Ce système joue également la carte de l’économie. D’une part, il permet d’utiliser un fil MIG, moins coûteux que les baguettes nécessaires au soudage TIG. D’autre part, il génère des gains sur le coût des matériaux. Puisque ce n’est plus la main qui tient le fil d’apport, le résidu de matière à jeter en fin de baguette devient moins important. En revanche, si cette solution convient bien pour les soudures linéaires, elle est moins adaptée aux endroits difficiles d’accès, du fait de son encombrement supérieur.
Différents procédés
D’autres méthodes de soudage à l’arc existent comme le soudage MMA dont la qualité du joint de soudure repose également sur la dextérité de l’opérateur. Ce procédé, connu sous le nom de soudage à l’arc à l’électrode enrobée ou soudage à la baguette, repose sur un câble de soudage et un porte-électrode dans lequel on glisse la baguette qui sert à la fois d’électrode et de métal d’apport. Lorsque cette électrode fusible touche le matériau à souder, l’arc est créé. L’intérêt de ce procédé est notamment de pouvoir être utilisé à l’extérieur, même en plein courant d’air, contrairement aux torches MIG et TIG, desquelles sort un gaz de protection. Si le vent balaie la protection gazeuse, la soudure devient poreuse et donc de mauvaise qualité. Dans le cas de l’électrode enrobée c’est l’enrobage qui, au fur et à mesure de la soudure, recouvre le joint de soudure en fusion et le protège.
Autre technique, le soudage plasma reprend le principe de la torche TIG. Mais au lieu d’utiliser un tungstène pour créer l’arc, ce dernier est provoqué par un faisceau laser à base de gaz. Très précis, le soudage plasma permet de travailler avec un faible ampérage (moins de deux ampères), ce qui le préconise lorsqu’un faible impact thermique est requis, sur des tôles très fines par exemple. Néanmoins, le marché de la torche plasma reste très minoritaire et sa commercialisation passe surtout par les constructeurs de poste à souder.
A noter également que les procédés MIG/MAG et TIG peuvent être raccordés à des robots de soudage ou à des systèmes automatisés, le poignet du soudeur étant remplacé par la machine. Néanmoins, contrairement à la situation dans d’autres pays européens, les équipements de soudage sont très peu automatisés en France.
Ampérage, diamètre, longueur
La méthode de soudage est choisie en fonction de l’application, autrement dit principalement d’après le matériau à souder et son épaisseur.
En fonction de l’ampérage requis, le corps de la torche peut atteindre des intensités plus ou moins élevées. La notion d’ampérage est liée directement à celle du diamètre du fil, qui dépend du volume de matière à apporter et donc de l’épaisseur de la tôle à souder. Ce dernier varie généralement entre 5/10, 6/10, 8/10, 10/10, 12/10 et 16/10. Dans le secteur automobile, par exemple, des petits diamètres sont essentiellement utilisés alors que pour des soudages de plus grande envergure avec des tôles épaisses, les grands diamètres sont privilégiés. Le cœur de marché est constitué par des fils de diamètres 10 et 12, ce qui implique des ampérages de 250 à 300 A. La capacité d’une torche MIG évolue généralement de 150 à 500 ampères, une torche TIG pouvant descendre à quelques ampères.
La longueur du fil d’apport joue également. Elle est déterminée par le lieu de travail. Si le soudeur opère en atelier, à proximité d’un générateur, les marques préconisent des torches conçues pour travailler avec des longueurs de fil de trois ou quatre mètres. En revanche, dès qu’il travaille sur des pièces importantes et n’a guère envie de déplacer le générateur, des longueurs de six ou huit mètres sont préférées. En matière de torches MIG, le cœur du marché se situe entre trois et cinq mètres.
L’échelle est un peu plus importante au niveau des torches TIG qui n’ont pas la contrainte de l’amené de fil automatique et acceptent donc des fils d’apport d’une longueur allant de trois à dix-huit mètres.
Refroidissement naturel et par eau
La notion d’ampérage implique un autre critère, valable tant pour les torches MIG/MAG que TIG, celui des systèmes à refroidissement naturel ou par eau.
Au-delà de 300 ou 400 ampères et pour grimper jusqu’à 500 voire 600 ampères, la torche doit être refroidie par eau. Acheminée par un tuyau incorporé, l’eau circule dans la torche en circuit fermé. Au moment où démarre l’arc, elle monte jusqu’au col de cygne et revient pour empêcher l’outil de chauffer.
Non seulement, le refroidissement par eau permet au soudeur de tenir une torche avec de forts ampérages, mais il influe également sur la qualité de l’arc. Si la la buse et le tube contact chauffent excessivement, la chaleur ne sera pas constante, ce qui peut impliquer des changements de paramètres sur l’arc.
Les systèmes à refroidissement par eau représentent environ 40% des ventes de torches MIG et TIG. Convenant à des applications considérées comme standard, donc plus nombreuses, les solutions à refroidissement naturel sont majoritaires.
A noter que la qualité des pièces d’usure, par exemple épaisseur et composition du cuivre, est également déterminante pour la qualité du joint de soudure, donnant à la torche les moyens d’envoyer une chaleur d’arc constante.
Ergonomie pour la torche MIG
Si l’on excepte les évolutions générées par les constructeurs de postes à souder qui, en faisant évoluer leurs produits, impliquent souvent des transformations au niveau de la torche, comme les commandes déportées à la poignée permettant au soudeur de régler la tension et la vitesse fil sans s’arrêter de souder et sans avoir besoin de revenir au générateur, les conditions de travail sont de plus en plus prises en compte. D’ailleurs, nombre de fabricants de torches participent désormais aux salons professionnels liés à la prévention des risques, ce qui n’était pas le cas auparavant.
L’enjeu est important. Entre la chaleur, les fumées, la nécessité de tenir en permanence la torche à la main, le métier de soudeur suppose de nombreuses contraintes. Faut-il s’étonner que selon la dernière enquête annuelle de Pôle Emploi « Besoins de main d’œuvre 2013 », l’industrie recherche actuellement plus de 4 000 soudeurs en France ? Par ailleurs, au-delà de leur responsabilité, les entreprises sont de plus en plus sensibles à ces aspects qui favorisent la réduction des arrêts de travail et améliore donc in fine la productivité.
En ce qui concerne la torche MIG, les réflexions empruntent plusieurs voies, à commencer par la légèreté. En une dizaine d’années, le poids de la torche a perdu 100 à 300 grammes, ce qui n’est évidemment pas neutre au bout du poignet du soudeur.
Plus que le poids, c’est la position dans laquelle le soudeur doit tenir sa torche pour travailler qui est susceptible de générer des troubles musculo-squelettiques et de la fatigue. Sont ainsi apparues des torches à l’ergonomie étudiée pour prendre en considération la position naturelle du poignet fortement sollicité lors de l’opération de soudage.
Les fabricants travaillent également sur la forme des cols de cygne pour trouver les meilleurs angles, de façon à ce que le coulissement du fil d’apport soit aisé pour éviter tout mouvement de pompage. Certains proposent des cols de cygne dont la conception est adaptée en fonction des travaux effectués, de façon à moins solliciter les muscles des soudeurs. Cette démarche, qui implique que le soudeur change de col de cygne en fonction de son travail, commence tout juste à entrer dans les mœurs du milieu de la soudure en France.
Maniabilité pour la torche TIG
En ce qui concerne la torche TIG, la tendance est à faire passer de plus en plus d’ampérage dans des torches de plus en plus petites. Mais c’est surtout la maniabilité du faisceau dans lequel transitent les divers câbles et conduits qui est travaillée. La prise en main de la torche TIG est en effet différente. Si la torche MIG s’utilise à pleine poignée et se dirige avec une main, la torche TIG est tenue souvent avec trois doigts comme si le soudeur utilisait un stylo. Les poignées sont donc souvent courtes et surtout, c’est la flexibilité du faisceau qui permet à la torche d’être manipulée facilement. Les fils de cuivre qui conduisent le courant sont par exemple tressés de manière à garder toute leur souplesse. Et le revêtement de protection des différents conduits (courant, gaz, eau) est conçu en silicone, moins rigide que le caoutchouc habituellement utilisé. La partie du faisceau la plus proche de la main du soudeur est même en cuir pour gagner encore en souplesse.
Certains fabricants ont également pris l’initiative d’éliminer du marché les électrodes radioactives, anticipant probablement une norme à venir comme c’est déjà le cas dans d’autres pays européens comme la Hollande, la Belgique, la Suisse. Cette mesure a été précipitée par la difficulté d’approvisionnement en électrodes, depuis les évènements de Fukushima, et facilitée par le fait qu’il existe de nouvelles alternatives, pas plus coûteuses et tout aussi performantes.
Aspiration des fumées
L’autre cheval de bataille des fabricants de torche concerne l’aspiration des fumées (cf. encadré), des démarches stimulées par la pression réglementaire même si aucune obligation légale n’est encore entrée en vigueur.
Les CRAM (caisses régionales de l’assurance maladie) et les services de l’hygiène et de la sécurité au travail préconisent une aspiration à la source dans laquelle s’inscrivent pleinement les torches. L’extrémité d’une torche MIG traditionnelle est alors équipée d’une buse qui permet d’aspirer les fumées à la production. Ce système est jugé très efficace puisqu’il permet de capter jusqu’à 99% des fumées de soudage émises. Il n’existe pas au niveau des torches TIG dont le procédé provoque moins de fumées et moins de poussières.
Pour la torche MIG, plusieurs systèmes sont en vigueur avec les procédés de la haute dépression et de la basse dépression. Le premier est le plus efficace, permettant d’aspirer la quasi-totalité des fumées, contre seulement 80% pour la basse dépression. Ensuite, l’aspiration s’effectue en haute dépression à une certaine distance des gaz de protection et ne risque donc pas d’absorber ces derniers, au détriment de la qualité de la soudure. Par ailleurs, ce procédé aspire de petites quantités d’air à grande vitesse – c’est l’inverse pour la basse dépression – et ne nécessite pas de tuyaux importants pour transporter les fumées, d’où une poignée plus petite et plus maniable même si elle reste plus conséquente que celle d’une torche non aspirante.
Ces préoccupations pour la santé du soudeur et de son environnement ont effectivement une contrepartie : alors que les fabricants travaillent sur des torches plus légères, les dispositifs d’aspiration contribuent à alourdir l’outil. Ce qui est parfois ressenti comme contraignant par le soudeur, comme d’ailleurs les autres dispositifs proposés qu’il s’agisse de la cagoule équipée d’un système d’aspiration ou le bras d’aspiration parfois lourd à déplacer... Néanmoins, les ventes de torches aspirantes sont en hausse, ce qui traduit bien une montée en puissance de ces préoccupations dans l’entreprise.
Quelle est la composition des fumées de soudage ?
Les fumées de soudage sont composées de gaz et de poussières :
Les gaz proviennent de la décomposition de l’air et contiennent en quantité variable du monoxyde de carbone (CO), de l’ozone (O3), des vapeurs nitreuses (dioxyde d’azote NO2, monoxyde d’azote NO), voire du phosgène (COCL2) lorsque la pièce à souder a précédemment été dégraissée avec des solvants chlorés ou autres produits de dégradation.
Les poussières inhalables sont celles provenant du métal soudé, du métal d’apport (80 à 90%) et de l’électrode. Elles sont donc extrêmement variées : aluminium, nickel, béryllium, cadmium, plomb, chrome, cobalt, cuivre, étain, fer, zinc, mobyldène, vanadium, manganèse, titane, silice (dans l’enrobage des électrodes enrobées).
Les risques ?
Les dangers sont variés en fonction de la nature du matériau soudé, du gaz utilisé, du métal d’apport…
Pour les soudages T.I.G et M.I.G, il existe un risque d’asphyxie provoqué par l’usage de gaz inertes lorsque ceux-ci sont mis en œuvre dans des espaces confinés.
Les fumées et les gaz peuvent provoquer des pathologies aigües (effets toxiques, irritants, allergisants) et chroniques (infections pulmonaires provoquées par les poussières).
Les principaux moyens de prévention ?
Les fumées de soudage sont nocives et doivent donc être captées à leur source d’émission en privilégiant, selon les procédés mis en œuvre et la configuration des pièces, les dispositifs de ventilation suivants :
• Cabine de soudage (la taille de la pièce à souder ne doit pas excéder celle de la cabine)
• Aspiration fixe à la source (table aspirante)
• Aspiration mobile à la source (tuyau flexible aspirant fixé sur une potence réglable suivant la localisation du cordon de soudure)
• Aspiration associée à l’outil ou à l’outillage (torche aspirante dont l’extrémité est équipée d’une buse d’aspiration des fumées adaptée aux systèmes MIG et MAG.
La gamme PSF
Centrovac d’Esab
avec système
d’aspiration des fumées.
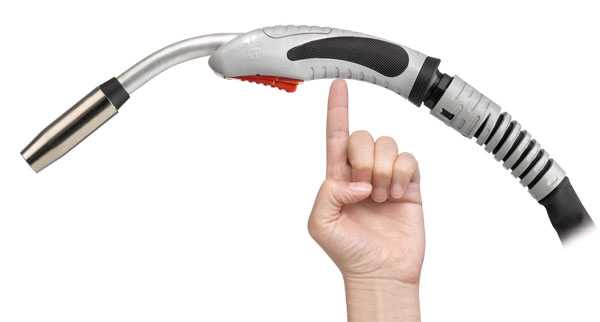
a obtenu un prix de l’innovation sur le salon
Industrie Paris 2012 pour sa poignée ergonomique
et la courbe arrondie du col de cygne, qui donne
une grande fluidité au coulissement des fils.
La nouvelle gamme de torche refroidie par air ABIMIG® A T de Binzel propose de nombreuses géométries de cols de cygne.
La torche PMT 42 W de Kemppi se caractérise
par sa conception légère
et ergonomique.
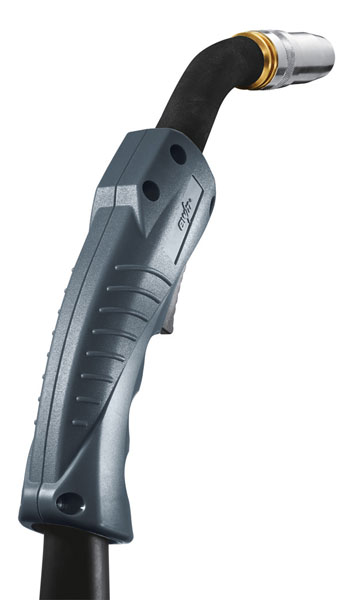
La série MT d’EWM se caractérise
notamment par un poids réduit,
ce qui facilite la manipulation
de la torche de soudage.